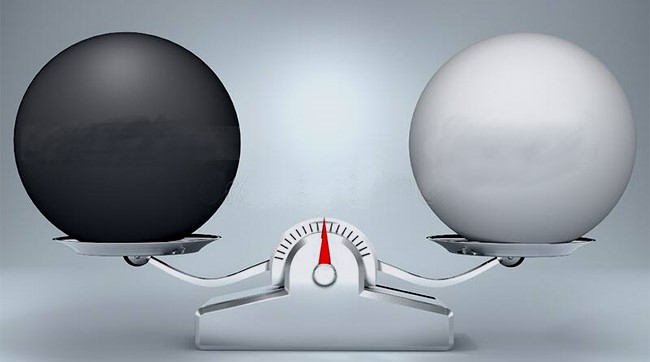
“How do we make this cost effective?“
A common phrase used amongst clients from all walks of life. The sayings “Buy once cry once” and “You get what you pay for” usually hold true, especially in real estate. While compromising on fundamental aspects such as location, structural integrity and other critical aspects of development are something that should never be done, there are an abundance of options available to achieve essentially the same result within a cost-effective manner through value engineering.
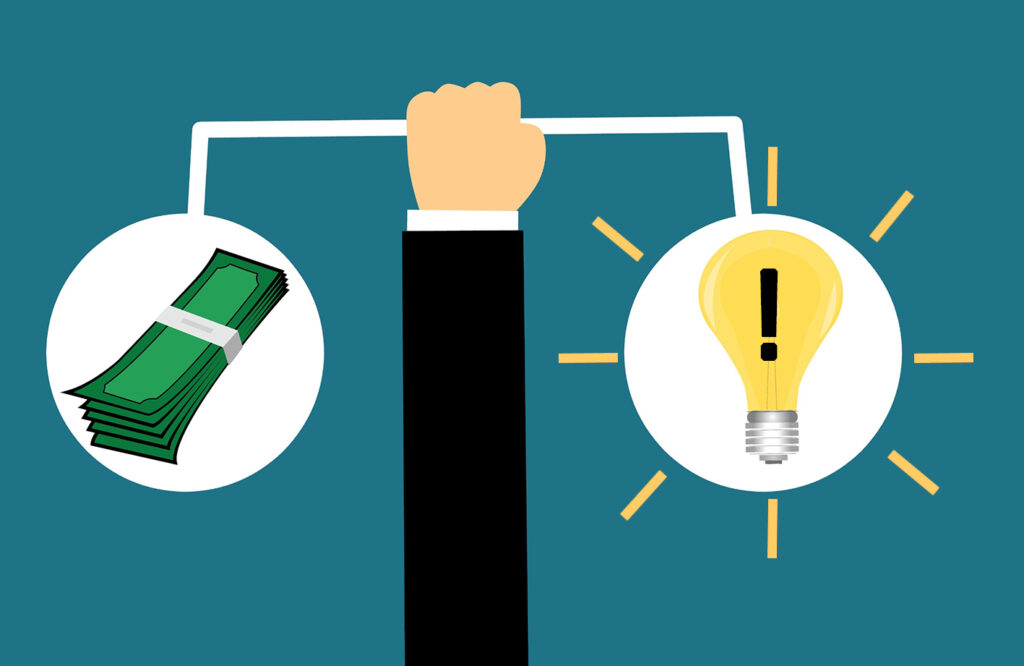
The opportunity cost
A negative connotation is usually associated with the term value engineering, for it tends to insinuate compromising on quality. However, this is not usually the case, for experienced developers can usually identify how to retrofit design and specifications to construct a quality product at a practical cost, avoiding financial burdens. The essence of value engineering is not to be wasteful when allocating capital to budget items and instead devise a more feasible plan for a similar result.
Be creative
Upon speaking with some local builders, they explained some ways they have implemented cost efficient alternatives for clients. A relatively new builder in Rye, who requested to remain anonymous, stated that his client wanted to incorporate accent walls throughout their home with expensive millwork. Due to the excessive cost, they instead created accent walls through routing drywall with LED lighting, trim and contrasting paint colors. “It was a creative approach to get the client what they wanted” he said, further noting that “it ended up looking so great, we will be using some of those features in our next project.” On a more substantial level, KOSL Building, a renowned residential builder, shared their insight on their value engineering approach. Mentioning that their take on VE is oriented towards holistic planning for longevity, “we always prep our homes for future amenities that require minimal invasiveness should they wish to implement that feature down the road. Some examples are a future elevator shaft where we have the footings prepped for the pit and align linen closets on each floor so that the space is currently usable and can be easily retrofitted at any point. Other minor examples are always leaving underground plumbing lines for future bathrooms/bars and sleeves to run wires throughout the house from basement to attic.” He elaborates that as people get acclimated to their home, there will always be something additional they may want to add. Having the main components already prepared for most features is half the battle and something they appreciate. Noting “We view those preparations as an accommodation rather than value engineering. Yes, it provides them with essentially a deferred cost savings if they wish to do it in the future, but true value engineering is done by modifying a significant scope to their benefit.” Having great experience with “thinking outside the box”, one instance involved modifying several poured concrete retaining walls into geogrid walls. “Although it took a bit longer, between drafting new plans, third part consultants and other factors, it was a significant savings.” Between the savings of concrete and stone veneer, the budget was reduced nearly in half. “We always have our client’s best interest in mind and build for longevity. If there is a cost-effective way to achieve that, we are happy to do it for them.”
Asses the pros and cons
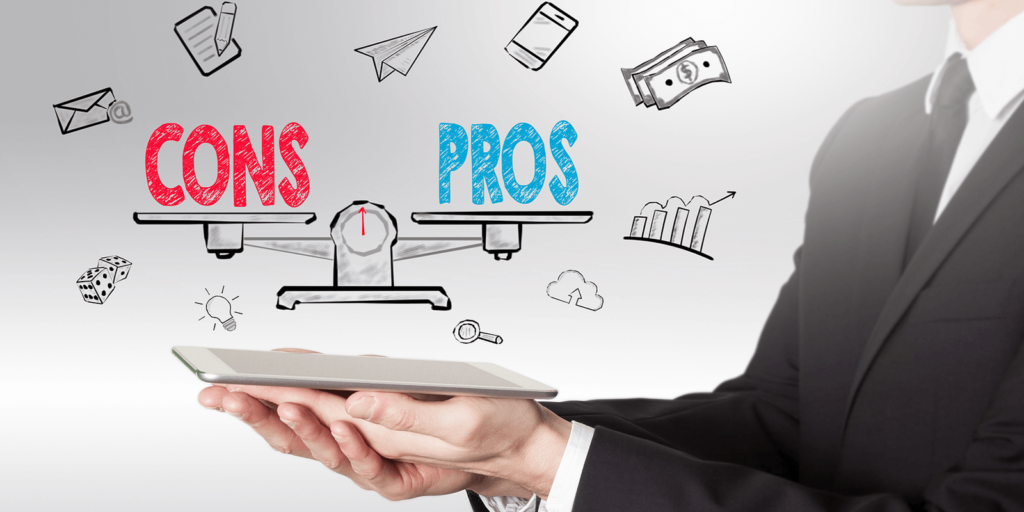
A critical aspect of creating a quality product is the knowledge and experience to know when certain items can be modified or not and if there are viable alternatives to accomplish the underlying goal of savings without compromise. The innovative world of value engineering will always continue to grow and thrive.
Have you ever integrated any value engineering? Comment below!
What are your mitigation strategies? Comment below!